Forklift Protection From High Heat and Extreme Cold
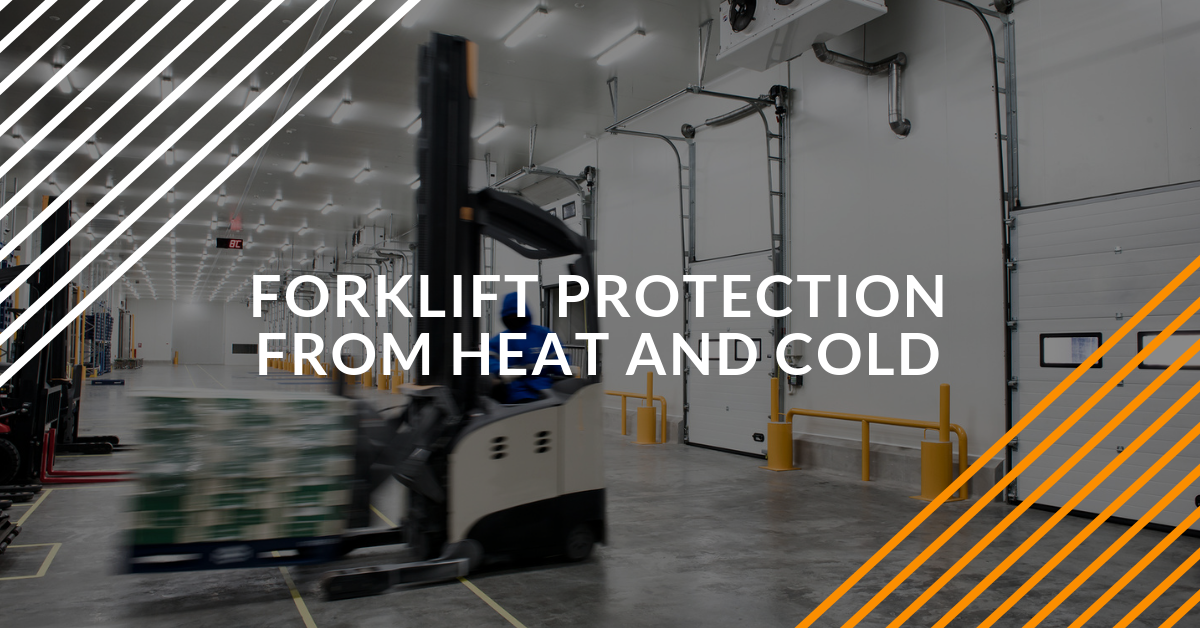
Protecting Against High Heat
Forklifts overheat for three reasons:
- Lack of maintenance. Overheating often results from low coolant levels, worn fans and hoses and clogged filters. Failure to clean or replace these and other basic parts can produce high temperatures that damage the forklift.
- Dirty work environment. Working outside can lead to dust and debris getting into the engine and other parts. A dirt yard or rough terrain can make it even worse. Even high ambient air temperatures can cause overheating.
- Improper operation. Misuse of a forklift, such as exceeding load lift capacity or driving too fast, can cause overheating. Riding the inching pedal can also cause heat problems as it slightly applies the brakes every time you use it.
The first rule of thumb for combatting high heat is to give your forklift frequent breaks and keep the fluids topped off. Also, most forklift manufacturers provide special tools and options designed to prevent overheating. Toyota offers two types: heat prevention and ventilation for cooling.
Heat prevention tools include:
- Foundry Package. This comes with three features:
- Heat-resistant sleeves to protect external wires and sensors
- Wrapping hydraulic cylinders in a heat-resistant material
- Providing a heat shield for mast hoses
- Perforated Belly Pan. This is designed to prevent hydraulic failures due to high ambient heat temperatures. It provides heat-resistant features found in the forging, foundry, and casting industries.
- Built-In Engine Protection. Toyota’s 8-series IC forklifts use the truck’s controller to monitor engine coolant temperatures. When it detects a malfunction, it limits the engine’s power to prevent further damage. It also reduces the possibility of failure due to prolonged use or operator error.
Cooling and ventilation tools include:
- High-capacity cooling package
- Premium-ventilation package
- Hood vents
- Vented radiator cover
- Perforated belly pan
- Dedicated transmission oil cooler
Be sure to check with your forklift provider for any special heat prevention tools, designs or packages they offer.
Avoiding the Deep Freeze
Extreme cold during winter can present a real risk when operating forklifts. Damage from exposure to extreme cold can result in high repair costs. It can also reduce productivity and workplace safety. The best way to protect against the cold is to get out of it after the work is over. When possible, avoid leaving forklifts overnight in freezing conditions. If this isn’t possible, try the following options:
- Always warm up electric forklifts before putting into full operation.
- Make sure diesel trucks have the right amount of antifreeze. This will prevent the liquid wax in the diesel fuel from turning into gel.
- Perform all preventive maintenance before winter sets in. A poorly maintained engine is more prone to malfunction in very cold weather.
- If you drive on roads or work in yards covered in snow, ice and mud, clean your forklift regularly to prevent blocked or clogged parts.
Outdoors isn’t the only place it gets cold. Working in refrigerated and frozen warehouses can also cause operational and safety hazards for forklifts. This includes costlier repairs, less than optimal operation, and shortened lifespans.
Condensation in the pin area is one of the biggest problems with indoor extreme cold. Yet, the problem doesn’t occur until the forklift comes out of the freezer. At that point, the truck begins to sweat as it warms up. The sweat seeps into pins in the wiring harness. The sweat then freezes the next time the truck enters the freezer. This causes the area to expand, which requires changing the connectors more often. The solution? Make sure any forklift you buy has a double-sealed connector design.
Next, “sweat the details.” In other words, pay attention to the little stuff that can make a big difference when dealing with extreme cold:
- Use the oils and greases your trucks need for top performance in harsh environments. They cost more to buy but will save money in the long run.
- Regularly check your switches and other electrical devices for moisture. Wet switches can freeze closed upon going into a freezer.
- Choose tires and batteries designed for extreme cold. Very low temperatures can reduce a regular battery’s capacity and run time by as much as 35%.
Staying Safe in Extreme Heat or Cold
To keep employees and trucks safe:
- Conduct full inspections of each truck every 250 to 500 hours of operation
- Make sure all parts are properly greased
- Keep floor surfaces clean
- Ventilate warehouses to minimize condensation when trucks come in from the outside
- Outfit forklifts with beacon lighting when working outside
- Keep warehouses well lit
Most important, make sure all truck operators are trained and certified to work in extreme conditions. It’s faster and costs less than you think!